背景課題生産ラインでの異常時対応や情報分析の効率化が求められていた
今回の事例で中心的な役割を果たしたのは、トヨタグループの源流である豊田自動織機からシステム開発チームが分社・独立して1991年に設立された、豊田ハイシステム(略称:THS)だ。同社は豊田自動織機をはじめとする製造業を中心に、流通業や医療・教育関連企業向けなどのシステム開発を手掛けるほか、パッケージソリューションやクラウドソリューション、組込みソフト開発など多彩な事業を展開している。
THSの事業の原点であり、現在でも大きな柱の一つとなっているのが、工場内の自働化・省力化を支援するFA(Factory Automation)システム。今回の見える化推進の取り組みも、そのFAシステムの延長線上にある。
豊田自動織機が生産する自動車やフォークリフト、エンジン、自動織機といった部品点数の多い機械類は、品物が流れていく間に何人もの作業員がそれぞれの工程を担当していく形の生産ラインで製造されるのが基本だ。こうした流れ作業の途中にトラブルが生じた場合、前後の工程にも大きく影響するため、作業員のボタン操作や各種センサーによる判定で、近くに設置された「アンドン」(ランプなどによる状態表示)から異常を周囲に知らせるのが一般的となっている。
「どれだけトラブルを減らす工夫を施しても、生産ラインで異常ゼロということはあり得ません。そのため、異常が生じたら可能な限り迅速に共有・対応できる仕組みがほしいと考えていたのです」と語るのは、THS トヨタシステム部 部長の市村伊左実氏だ。
異常時にはアンドンの情報に従ってラインの流れを止めるなどの対応がとられるが、現場で容易に対処できると判断された場合には現場での対処が優先され、工場全体を管轄する生産管理部門や生産技術部門などへの報告が事後になる場合もあったという。しかし、生産ラインは最大限の生産効率を目指しているものだけに、ちょっとした停止でも遅れを取り戻すことが容易ではなく、納品が遅れたり、計画していた生産数を達成するために残業が発生したりと、生産・労務管理にも影響を与えていた。
また一方で、現場の生産記録が集約されていないという課題もあった。工程管理、生産情報、品質情報、設備情報など、それぞれの目的に応じて個別のシステムが構築されてきたため、現場から得られた情報が各システムに分散していたのだ。例えば、ある品物で品質上の問題が発見され、状況を分析して対策を講じるといった場合には、その品物に関する実績情報を各システムから必要な情報を抽出・収集してこなければならず、時間と手間を要していた。
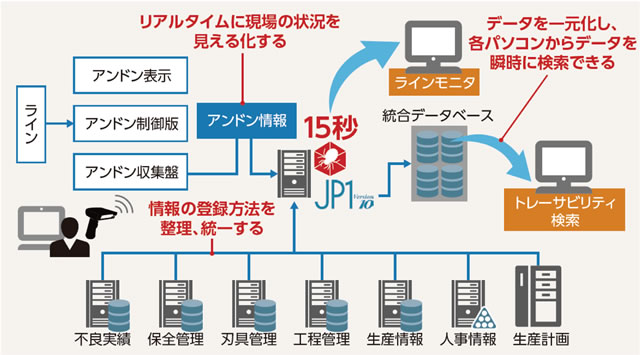